by UniversalTube | May 19, 2025 | News
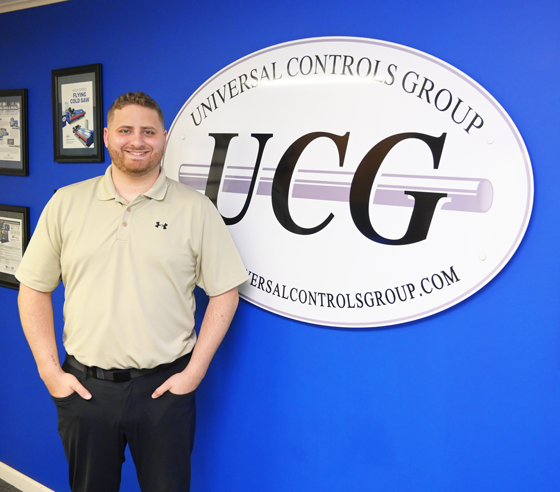 |
We’re excited to welcome Jake Steiner to Universal, joining our machinery sales team alongside Chris Thompson. With a strong background in industrial and material handling since 2015, Jake brings proven success in sales, marketing, and project management. Jake speaks both English and Spanish, which will help strengthen our relationships with Spanish-speaking customers and enhance communication across our existing markets. His focus on communication, customer satisfaction, and creative marketing will make it easier than ever to connect with Universal. Jake is ready to help you find the right equipment and support your manufacturing goals. Contact him at +1 (419) 872-2364 or jake@utubeonline.com. Universal has grown into a leading supplier of new and used metalworking machinery, with one of the largest inventories in the industry. We offer machine reconditioning, new controls and drive systems, start-up support, and options to buy or sell surplus equipment. Founded in 1984 by Ralph Girkins, Universal specializes in tube mills, rollformers, coil handling machinery, auxiliary equipment and more—sold as-is or reconditioned by our expert team. We also build custom lines using equipment from our inventory or new machinery by Universal Controls Group (UCG) and ERWTech. Since merging with UCG in 2020, we’ve continued expanding our capabilities to better serve our growing and diverse customer base. +1 (419) 872-2364 sales@utubeonline.com |
by UniversalTube | Apr 24, 2025 | News
In-stock, economical, custom, and fully supported rollforming lines
Universal is your one source for custom rollforming lines. We can reconfigure, upgrade, and integrate equipment from our floor to build a line tailored to your specific part.
Our large inventory of rollformers and line equipment is available as-is, or with options like reconditioning, new controls, drive systems, electrical start-up, warranty, and more.
Contact us to discuss your requirements: 1-419-872-2364
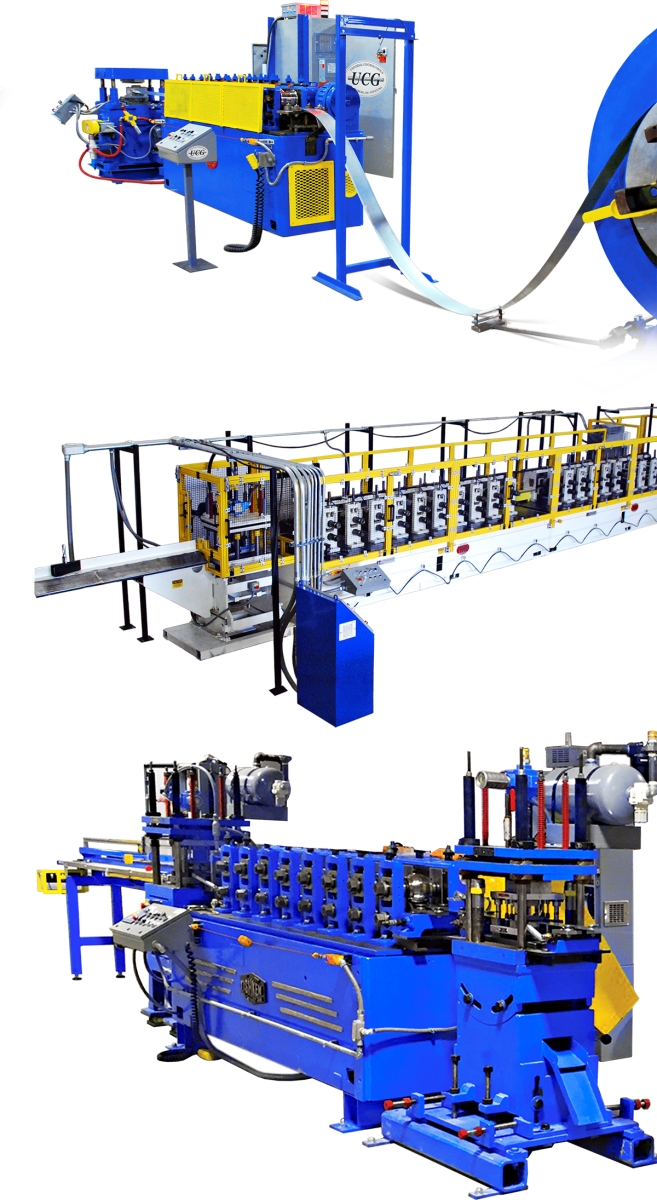
by UniversalTube | Mar 4, 2025 | News
Universal is excited to exhibit at Fabtech Mexico, taking place May 6-8, 2025 at Cintermex in Monterrey. As a leader in new and used tube mills, rollformers, coil handling equipment, and metalworking machinery, we’re bringing our expertise and extensive inventory to the show.
Forming & Fabricating, Booth #111 – Stop by to explore our in-stock machinery, discuss custom automation solutions, and learn how our service and support set us apart. Whether you’re looking for a complete production line or an upgrade to your existing setup, we have the right solution for you.
We service what we sell – Our team is ready to help with replacement parts, automation control upgrades, technical support, and more to keep your operation running efficiently.
Make sure to connect with us at Fabtech Mexico! Contact us today to schedule a meeting and see how we can help improve your production.
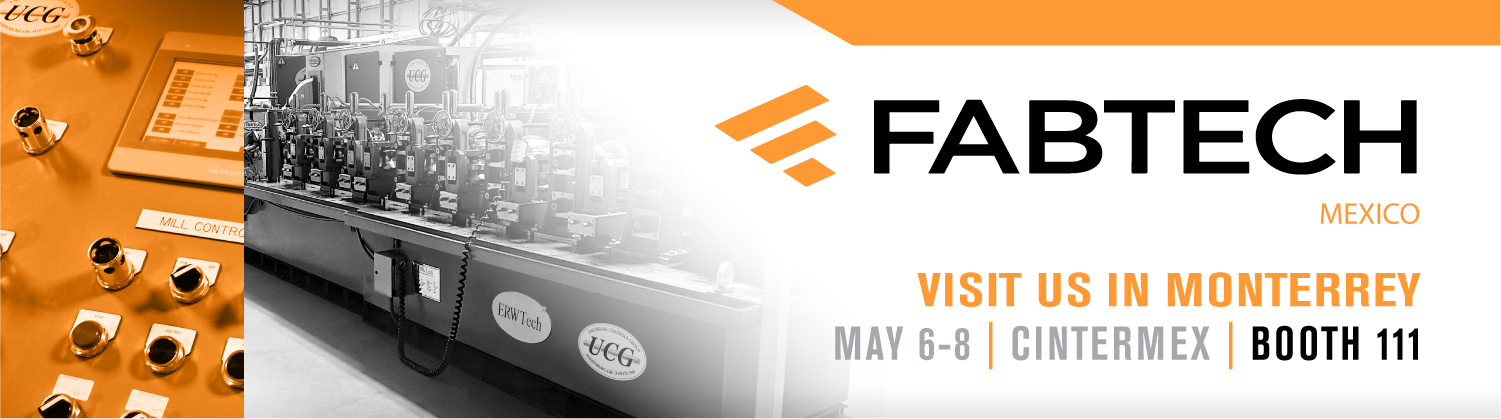
by UniversalTube | Jan 22, 2025 | News
This year, Universal Tube & Rollform Equipment Company marks 40 years in the metalworking industry, while Universal Controls Group, celebrates 20 years of delivering cutting-edge automation solutions. Together, we’ve provided reliable machinery and automation systems that have helped our customers achieve lasting success.
Universal Tube & Rollform Equipment Company: 40 Years of Excellence
Since 1985, Universal Tube & Rollform Equipment Company has been a trusted supplier of quality metalworking machinery. We offer a variety of new, used, and reconditioned equipment, including tube mills, roll formers, and coil handling systems, ensuring our customers meet their production goals while keeping costs manageable.
Universal Controls Group: 20 Years of Automation Excellence
Founded in 2005, Universal Controls Group has specialized in designing and implementing control and drive systems that optimize machinery performance. From custom control panels to proprietary systems like U-Trak and U-Cut, our automation solutions improve efficiency, precision, and operational ease across a range of industries.
Looking Ahead
As we celebrate these milestones, we thank our customers, partners, and employees for their continued support. We’re committed to driving innovation and supporting the growth of the metalworking industry for many more years to come.
Here’s to 40 and 20 years of excellence—and many more to come!
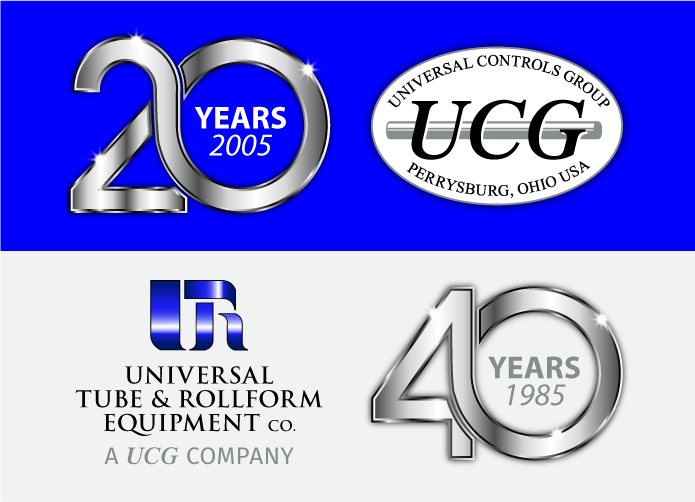
by UniversalTube | Jan 2, 2025 | News
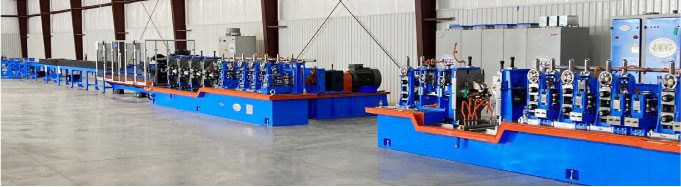
New UCG machinery is built to boost productivity and deliver reliable, long-lasting performance. Our support team ensures your equipment stays efficient, minimizing downtime throughout its lifecycle. To enhance this commitment, we’ve added a dedicated service department focused exclusively on maintaining the new machinery we sell. Here’s how we support you every step of the way:
Technical Support
Whether you need troubleshooting assistance or have operational questions, our expert team is ready to provide prompt, accurate solutions over the phone.
On-Site Support
When technical support alone isn’t enough, our skilled technicians are ready to visit your facility. They’ll diagnose issues firsthand and implement effective fixes to get your operations back on track quickly and efficiently.
Replacement Parts
Access to replacement parts is essential for maintaining performance. We supply quality replacement components, ensuring compatibility and reliability for the equipment we provide.
Maintenance Services
Regular upkeep is key to extending the life of your machinery. Our maintenance programs are tailored to your needs, helping to prevent unexpected breakdowns and maintain peak efficiency.
UCG is more than a supplier; we are your partner in success. With the addition of our dedicated service department, we’re better equipped than ever to keep your machinery running smoothly so you can focus on delivering superior products to your customers.
Contact us to learn more about our services and how we can help keep your new manufacturing machinery in top condition. Let’s work together to build a seamless production experience.
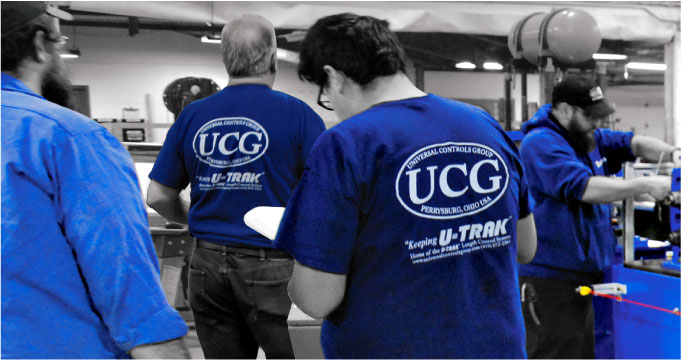
by UniversalTube | Oct 28, 2024 | News
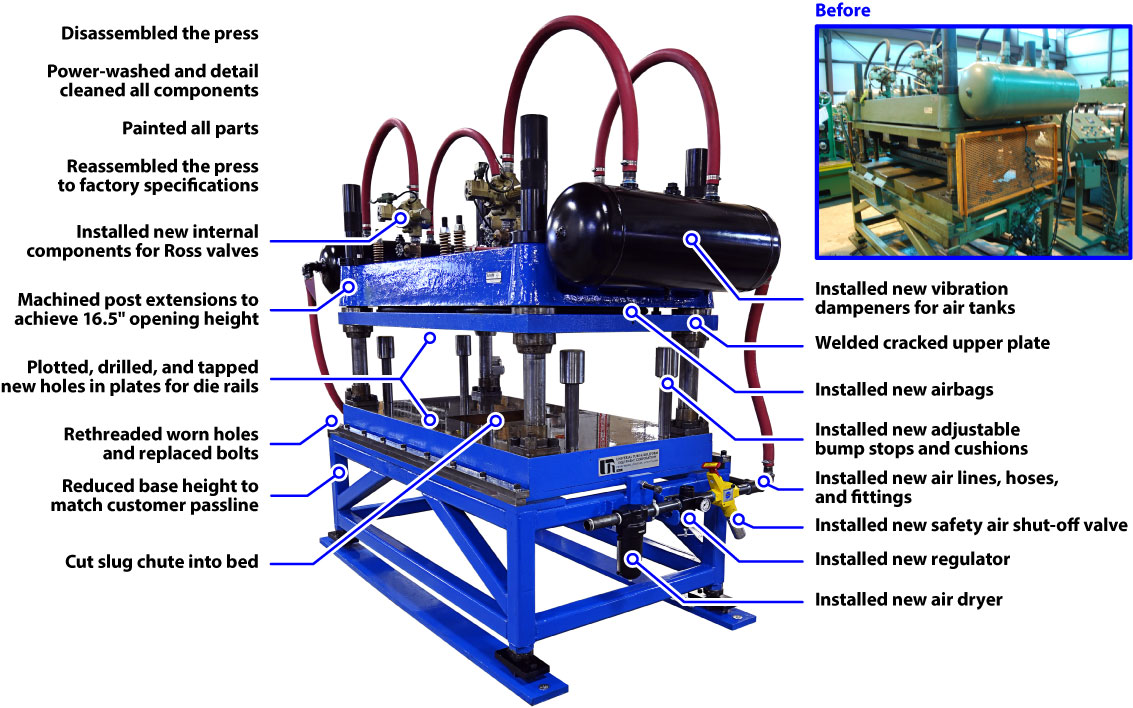
Universal offers a large selection of industrial machinery, with options available both as-is and fully reconditioned to fit diverse operational needs. Recently, our expert team reconditioned a cut-off press machine, restoring it to optimal running condition and showcasing our reconditioning capabilities.
Complete Overhaul
The process began with disassembling the press, followed by power-washing and detail-cleaning all components. We then painted the parts and reassembled the machine to factory specifications.
Repairs and Modifications
Key repairs included certified welding of a cracked upper plate and rethreading worn holes. We modified the base height to meet the customer’s passline requirements, machined post extensions to create a 16.5″ opening height, cut a slug chute into the bed, and added new holes for die rails.
New Replacement Parts
The machine was outfitted with new airbags, internal components for Ross valves, vibration dampeners, air lines, an upgraded regulator, air dryer, adjustable bump stops, cushions, and a safety air shut-off valve.
Testing
After reconditioning, we conducted a comprehensive functionality test to ensure reliable operation.
Explore Our Inventory and Services
With one of the largest inventories of used tube, pipe, and rollform machinery, Universal offers flexible options for purchasing equipment as-is or fully reconditioned. Contact us to discuss your equipment needs or learn more about our reconditioning services: +1 (419) 872-2364.
Page 1 of 712345...»Last »